History of washi-making: from the origin to introduction of Japanese style washi-making
Washi (Japanese paper) has been made from the ancient times in Japan.
In around 610 AD, the technique of hand making paper was brought from Korea by Buddhist monks, according to the Nihon-Shoki, also known as The Chronicles of Japan, one of the oldest books on classical Japanese history.
Washi was introduced in the era of Shotoku Taishi (Prince Shotoku).
It is believed that Shotoku-Taishi first took an interest in the washi making technique and popularized it for Syakyo (hand-copying of sutra) to propagate Buddhism.
Afterwards, the washi was used for management of family registration by the Japanese government who intended to progress the centralization, and it was made by state-run paper stores, “Kamiyain”.
In the Heian Period (710-794), a unique Japanese culture was gradually established in the literature world, and Japanese style paper-making method called “Nagashisuki” was introduced.
With this method, washi texture and durability largely improved and became softer and stronger.
Washi developed its quality to the extent that nothing is comparable in the world.
Papers were valuable, so that washi was recycled, using the technique, “Sukikaeshi.”
Used papers were dissolved, and remanufactured.
During the Kamakura Period (1192-1333), which featured a warrior culture, washi was used for gifts exchanged between warriors.
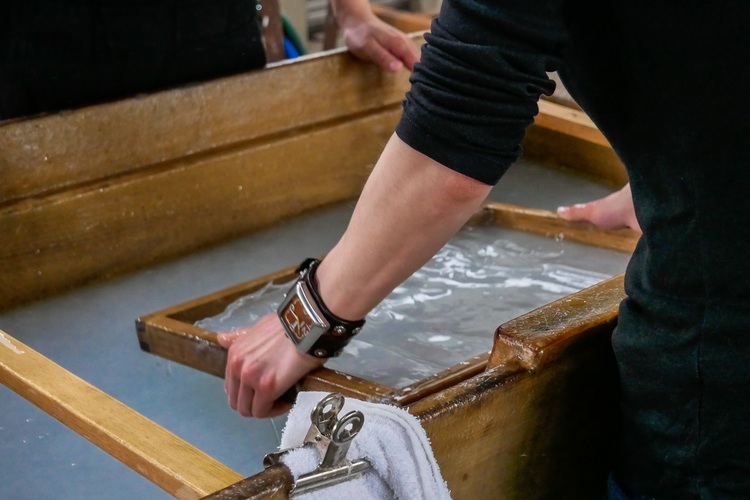
Washi from the Edo Period to date
In the Edo Period(1603-1867), washi rapidly prevailed all over Japan in line with the flourishing common-people based culture.
Behind the scenes, washi supported the development of various entertainment, such as Ukiyo-e or Nishikie.
In Osaka, a distribution base for rice and local specialties, washi was one of the most popular products after rice, and was sold by many traders.
As the demand grew, many feudal domains started to produce the Japanese papers.
It was highly regarded as a convenience as farmers can make it even during winter to make the most of their agricultural off-season so as to turn the goods into money.
In the Meiji Period(1867-1912), Japan started to import western papers made with pulp from America and Europe, which led to the modernization of Japanese paper production system from the monopoly system to the non-monopoly.
To fight against the mass produced western papers with high suitability for printing, more durable washi was invented.
Despite being pressurized, washi-producers managed to maintain the same volume of their production.
The turning point was during the period of rapid economic growth after the World War II.
The advance of mechanization promoted mass production rapidly, which caused a decline in the manual making.
What makes matters worse, the depopulation of the washi making areas led to a shortage of successors, and the popularity of western umbrellas caused a decline in the Japanese washi umbrella.
The same problems also attacked raw material producing areas, triggering unstable production.
However, history repeats itself.
Modern people started to pay attention to the valuable elements of washi, such as uniqueness, flexibility, and durability. It is now in the limelight.
Washi is considered to be the most durable paper in the world, and was employed for the conservation work of “The Last Judgement” at the Sistine Chapel in the Vatican.
Washi has registered as a UNESCO intangible cultural heritage as well.
Washi shines through over times with consistent problems for many centuries, such as a shortage of successors for making it.
How to make washi and what is the material
Washi has been made since the ancient times.
In the process of washi-making, tree bark is boiled in order to extract the necessary fibers.
The removed fibers become the main material for washi.
Before learning more details on washi-making, let me explain the key plants for washi.
The hemp and the mulberry family were widely used in the past.
During centuries, a variety of materials were tested.
After the experimentation, washi makers started to use kouzo, mitsumata, and a shrub called ganpi primarily.
C haracteristics of kouzo and main producing areas
Kouzo, one of the mulberry family, grows as tall as 3 meters.
It grows well, and the fibers from the inner bark (Jinpi) is thick and long, which is the key material for washi.
The length of the fiber is from 5mm to 20mm.
The strength is robust to the extent which the long strands of the fibers are not easily broken throughout the sieving process as the strands are carefully bound together, so that kouzo helps to boost the durability of washi.
For this reason, Kouzo is widely used for various papers, such as sliding screen papers, paper-hangers, and art papers.
Nowadays, kouzo is the most sought-after material for washi.
Motoyama town of Kouchi prefecture and Daiko town of Ibaraki prefecture are home to kouzo, accounting for most of the domestic production.
Particularly, “Nasukozo” produced in Daiko town is highly recognized amongst Japanese washi producers.
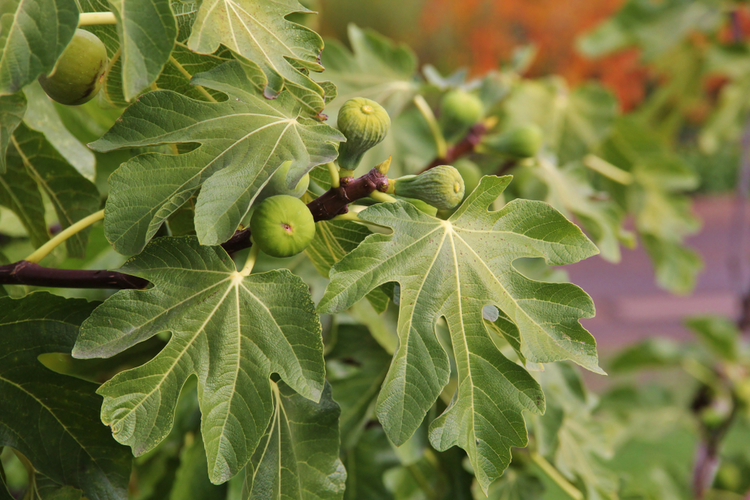
Characteristics of mitsumata and main producing areas
Mitsumata is relatively new material compared to others.
Paper producers started to use it 400 or 500 years ago.
An old book published in 1598 stated that mitsumata is used as a material of washi.
An interesting fact is that Japanese people were not able to distinguish mitsumata from ganpi (mentioned later) until the paper making technique was introduced.
Because the both are the daphne family.
Apparently, the implementation of mitsumata dates back to the Meiji Period (1868-1912), and it was mainly used at print offices.
The name of mitsumata is a dialect of Chubu region.
Mitsumata, which belongs to the daphne family, gets its name from its branches, which each grow in three sections.
The adult trees grow up to 2 meters for three years.
Currently, Okayama prefecture is the No.1 producer nationally.
However, the production volume has fallen year by year due to the mounting depopulation and aging of the growers.
The surface of washi made with mitsumata, is smooth, delicate, elegant and glossy.
All the brilliance comes from the flexible and thin fibers.
With this fantastic quality, it is used for Japanese banknotes.
Also, it is used for a special washi inlaying gold leaves or silver leaves, and washi for Japanese calligraphy.
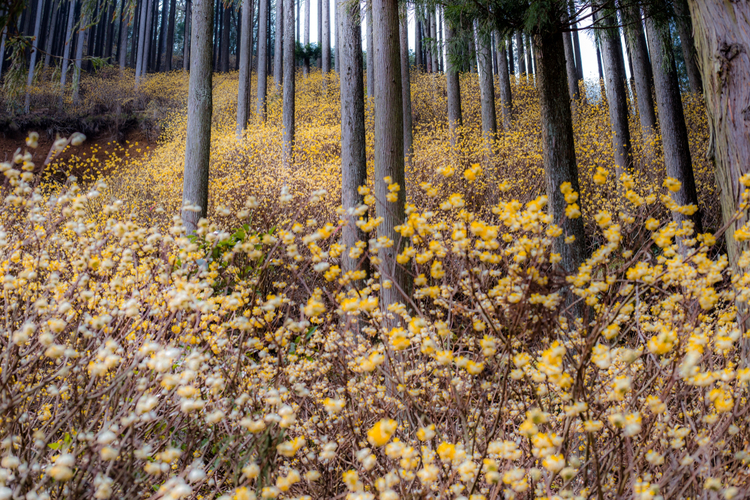
Characteristics of ganpi and main producing areas
Ganpi is from the same daphne family as mitsumata.
It is a brilliant material to produce glossy papers because of its thin fibers. .
However, it grows slowly and the cultivation is not easy, so that it is not normally grown at farms.
The ganpi seen in the current market is indigenous.
After the harvest, the bark is removed from the wild-grown gampi trees.
The main producing area is around Mt. Sanuki in Tokushima prefecture.
Washi made with ganpi features a combined strength, which comes from kozo’s durability and mitsumata’s brilliance.
Ganpi fibers are short and thin, semi-transparent and glossy, and don’t attract insects, hence, it is suitable for repairs of cultural properties.
This is the beauty of gampi.
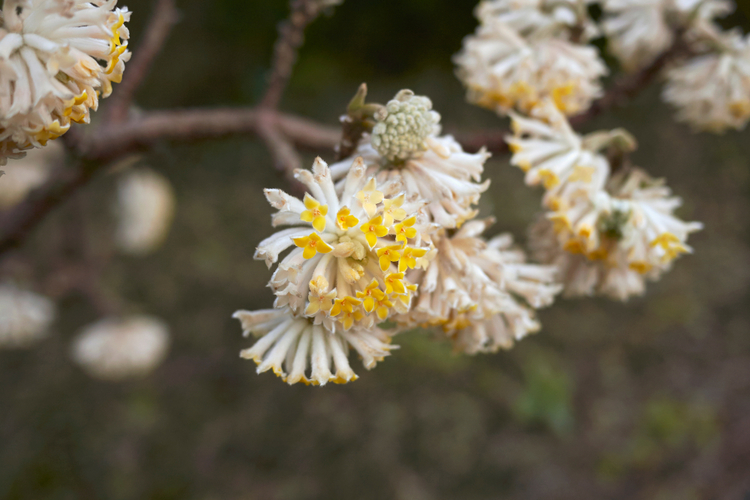
conclusion
Washi has been produced from ancient times in Japan, and today, the value of the washi is highly recognized.
In the past, various trees were used for washi-making.
Today, washi made with kouzo, mitsumata or ganpi significantly contribute to our modern life in various forms, such as sliding door papers, calligraphy papers, Japanese banknotes, and repairs of cultural properties.
We should deepen our knowledge of the washi, and need to pass down the wonderful traditional culture to the next generation.